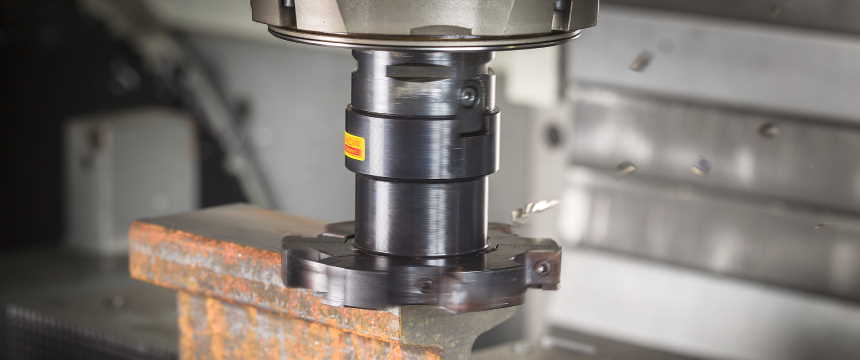
Gestión de incidencias con Corek
¿Tiene problemas con el servicio al cliente? ¿Conoce las incidencias que se producen en la planta de producción y las consecuencias que están suponiendo? ¿Desea avanzar en la mejora continua de su empresa? ¿Sabe que implantando un sistema de gestión de incidencias puede dar pasos hacia la excelencia?
¿Qué es una incidencia?
Una incidencia es cualquier suceso que afecta directa o indirectamente a la buena marcha de las actividades de la empresa.
Las incidencias se pueden originar por falta de información, problemas con las máquinas o con la materia prima, una deficiente ejecución de algún trabajo, etc.
En todas las organizaciones se producen incidencias, la diferencia entre unas y otras radica en cómo se gestionan. Lo más urgente es tratar de solucionarla lo antes posible para salir del paso y poder continuar. Sin embargo, los talleres mejor organizados van un paso más allá, implantando un Sistema de Gestión de Incidencias. Este sistema nos sirve para analizar las incidencias e identificar la causa última de que se hayan producido. Conociendo las causas podemos tomar las decisiones adecuadas para neutralizarlas y evitar nuevas incidencias.
Objetivo
El objetivo principal es reducir el número y la gravedad de las incidencias producidas en la planta. Para conseguirlo, hay que dar 3 pasos:
- Registrar las incidencias.
- Analizarlas y determinar la causa que las ha originado.
- Tomar las decisiones y acciones necesarias para que no se vuelvan a producir, o al menos para que lo hagan con menos frecuencia.
Estos pasos deben hacerse de forma sistemática, no puntual, estableciendo un procedimiento de trabajo donde se defina la periodicidad con que se revisan las incidencias, el responsable de hacerlo y la forma de actuar.
Ejemplo: revisión semanal, los viernes a las 12:00 por parte del jefe de taller. Consultará con todos los implicados para aclarar lo ocurrido y determinar la causa. Las decisiones tomadas para evitar que se repita se deben registrar en la misma incidencia y transmitir a todo el taller por escrito en el tablón de comunicaciones.
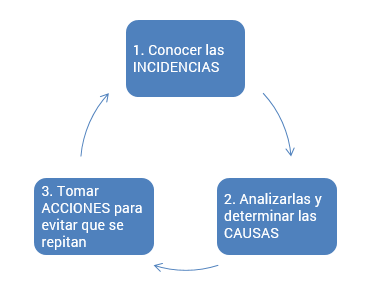
Condiciones
Es importante recalcar que para que el sistema funcione bien son necesarios tres elementos
A. Trabajo en equipo.
Es necesaria la implicación de todas las personas afectadas y el compromiso expreso de la dirección. Hay que prestar especial atención a la comunicación, creando una cultura de transparencia e información de las acciones que se llevan a cabo. Nunca se debe “culpar al mensajero”.
B. Sistema de información: Corek ERP.
Corek permite tener la información bien estructurada: orígenes, tipos y causas de incidencias, órdenes de fabricación, recursos implicados, estados de las incidencias, etc. Facilita el registro y gestión de las incidencias. Ayuda a valorar su coste. Aporta información de Para evaluar los procesos y las acciones de mejora debemos disponer de información fiable, que también puede aportar Corek ERP con su Panel de Mando el Informe Semanal y los listados de gestión de incidencias.
C. Metodología.
Se necesita establecer unos procedimientos claros a seguir y ser disciplinado. Las responsabilidades se deben definir con claridad.
1. Registro de incidencias
Este primer paso es imprescindible, ya que si no se registran no se conocen y no podemos actuar. Lo más efectivo y deseable es que las registre la persona que las detecta.
Corek facilita el registro de incidencias por parte de los operarios de planta mediante Corek Factory. Se pueden registrar cuando se registra el cierre de una trabajo. Deben clasificarla y pueden introducir una explicación personalizada de lo ocurrido.
También puede indicarse información adicional como si se han rechazado piezas o el tiempo dedicado a la incidencia. Posteriormente Corek utilizará esta información para valorar el coste económico de la incidencia.
Incidencias registradas automáticamente
Corek genera incidencias de forma automática cuando se producen las siguientes situaciones:
- Rechazo de piezas semielaboradas durante la fabricación.
- Rechazo de piezas terminadas. Pueden rechazarse tras detectar que no son conformes o tras una devolución de cliente. (Producto No Conforme).
- Devoluciones de cliente.
- Tareas de reparación.
Las tareas de reparación se pueden crear directamente por los operarios en Corek Factory o en la oficina técnica tras una devolución. Otras situaciones que generan incidencias si se configura:
- OFs cerradas con una desviación de tiempo de trabajo superior a un valor.
- OFs cerradas con una desviación del coste estándar superior a un valor.
- Disponibilidad de un recurso inferior a un % durante una semana.
- Eficiencia de un recurso inferior a un % durante una semana.
2. Determinación de la causa
Una vez generada, la incidencia permanece en estado ABIERTA, para que sea revisada por el responsable. Durante la revisión se debe analizar lo que ha ocurrido, hablando con las personas directamente implicadas para establecer la CAUSA que ha llevado a que ocurra. Tras establecer la causa, la incidencia se puede dar por CERRADA.
Opcionalmente, se pueden registrar anotaciones sobre el análisis realizado y también una respuesta para la persona que registró la incidencia.

KPIs de incidencias
Pada poder gestionar y hacer seguimiento de la gestión de incidencias, Corek aporta varios Indicadores Clave o KPIs, que se pueden configurar a la medida del cliente. Estos KPIs se pueden consultar tanto en el Panel de Mando General como en el de Producción.
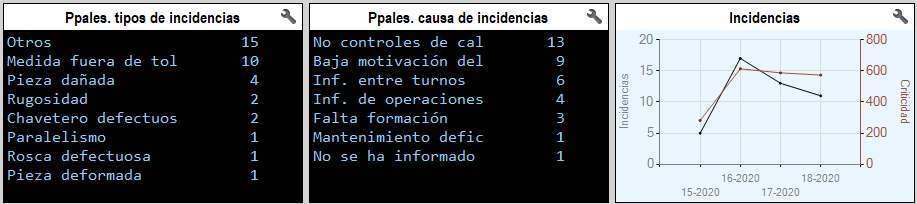
Clasificación de incidencias
Las incidencias se clasifican por su origen y su tipo, siendo configurables ambas listas. El tipo de incidencia depende del origen.
- Defecto en la pieza *
- Medida fuera de tolerancia
- Chavetero defectuoso
- Cilindridad / concentricidad
- Planitud/perpendicularidad/paralelismo
- Paralelismo
- Piezas deformadas
- Pieza dañada
- Pieza deformada
- Pieza rayada
- Pieza golpeada
- Rosca defectuosa
- Rugosidad
- Soldadura defectuosa
- Tratamiento defectuoso
- Falta información
- Plano incompleto
- Falta información en la OF
- Faltan operaciones en HdR
- Problema con MP
- Falta material
- Material defectuoso
- Problema con máquina
- Posible avería
- Mal calibrada
- Problema con herramientas/utillaje
- No hay herramienta o utillaje
- Herramienta mal calibrada
- Herramienta rota
- Problema en el proceso
- Vibraciones
- Formación de rebabas
- Rompe mucha plaquita
- Automático
- OF desviación en coste
- OF desviación en tiempo
- Eficiencia de un recurso
- Disponibilidad de un recurso